Plastic recycling is commonplace but imperfect. Part of the problem, says Dr. Jason Bara, is that current processes yield lower-quality plastics with reduced value and fewer end uses. In a circular plastic economy, any plastic could be broken down to its component parts and then reconstituted into new products with little or no waste.
The science is not there yet, but it may be one step closer.
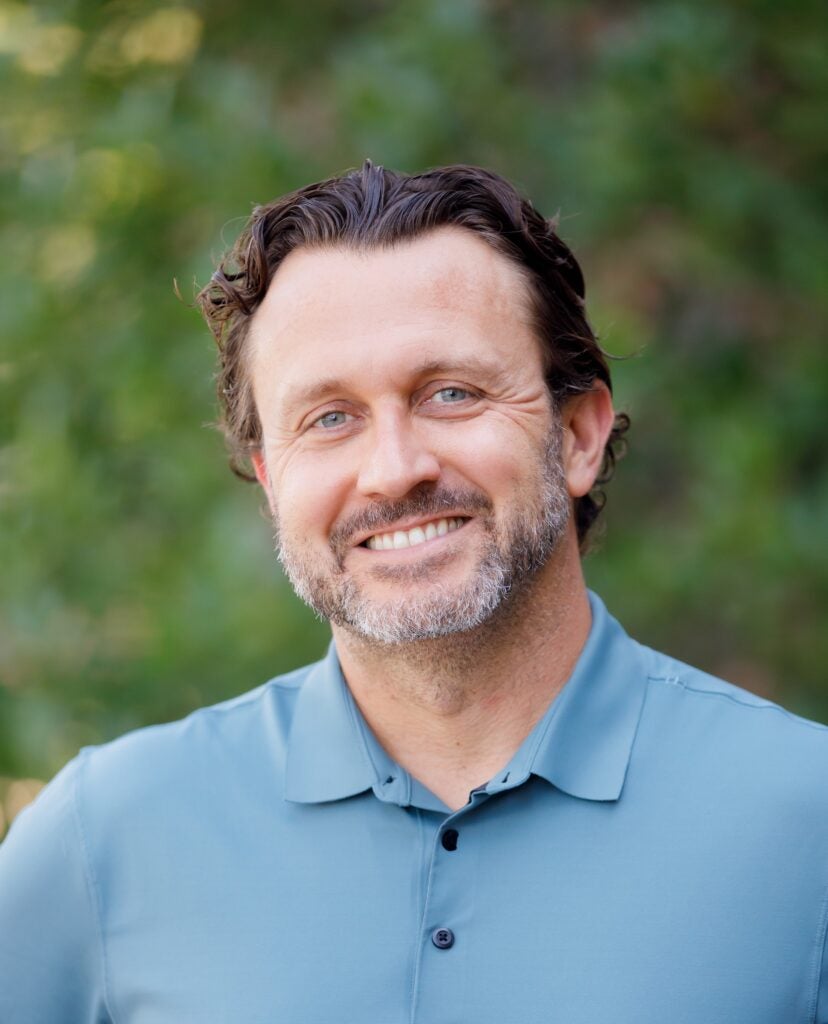
Bara, a professor in the College of Engineering, leads a team at The University of Alabama working to improve methods to recycle the ubiquitous plastics we interact with daily.
Polyethylene terephthalate (PET) is a common plastic that responds well to chemolysis, a chemical process that depolymerizes plastic for recycling. Much of the previous work on chemolysis and PET has focused on water, alcohols, and amines. Amines are a group of compounds derived from ammonia and are especially effective for PET depolymerization, but most products formed from the aminolysis of PET have limited uses, Bara said.
“Let’s See What Happens”
Nothing in the literature pointed to the effectiveness of imidazoles in this process. Imidazole, and its related compounds, are a group of organic molecules that are used in a wide range of applications and even appear within biologically important compounds.
“I’ve been working with imidazole for much of my career,” said Bara. “It’s pretty amazing how versatile it is.” Bara had been working for two years with using amines to break down plastics as part of a National Science Foundation grant geared toward reducing plastic waste. His appreciation for imidazole’s versatility made it a natural extension to see what happened when he tried using it for chemolysis.
“My student came back into the lab and said oh — the plastic is gone. It’s all gone.”
The University of Alabama has filed a patent application for the process, which offers several key advantages over other chemical recycling methods for PET. Among these is the lack of need of an additional solvent or catalyst because imidazole has a relatively low melting point. These are favorable qualities for developing a cost efficient and commercially viable process.
Breaking down PET via imidazolysis yields chemical intermediates that can be transformed to a range of other chemicals that are hard to get by traditional methods.
“Our imidazolysis process is unique in that it’s a flexible recycling technology, and you can get a wider range of final products from PET depolymerization when you do it our way,” Bara said.
Chasing the Next Challenge
Bara says one of the more exciting things about the research is what lies ahead.
PET is among the easier plastics to recycle. For one thing, it is relatively clean because it is used in food containers and drink bottles, and it generally contains few additives. Based on their results so far, imidazolysis is also useful in depolymerizing polyurethanes, which are trickier to work with than PET.
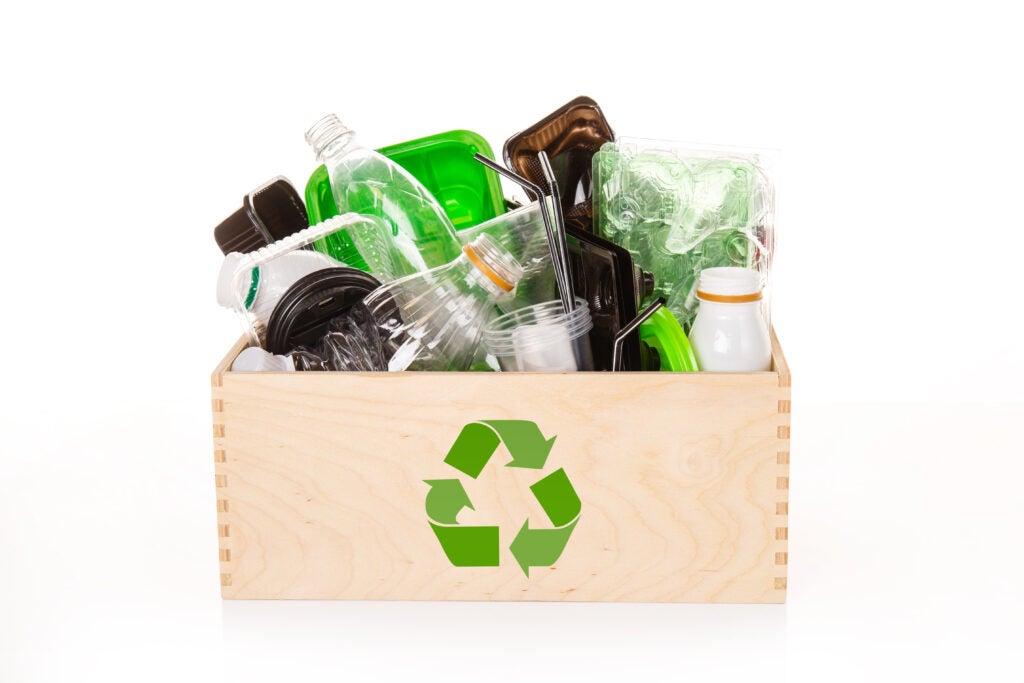
“There is generally good awareness around the need to recycle plastics and other materials (paper, metal) that commonly go into our recycling bins,” he said. “But it’s harder to appreciate that polyurethanes can also be chemically recycled.”
Polyurethanes are generally encountered as foams that are full of air, do not melt and often are formulated with any number of inorganic additives. Think packing foams, seat cushions, memory foam mattresses and automobile seats.
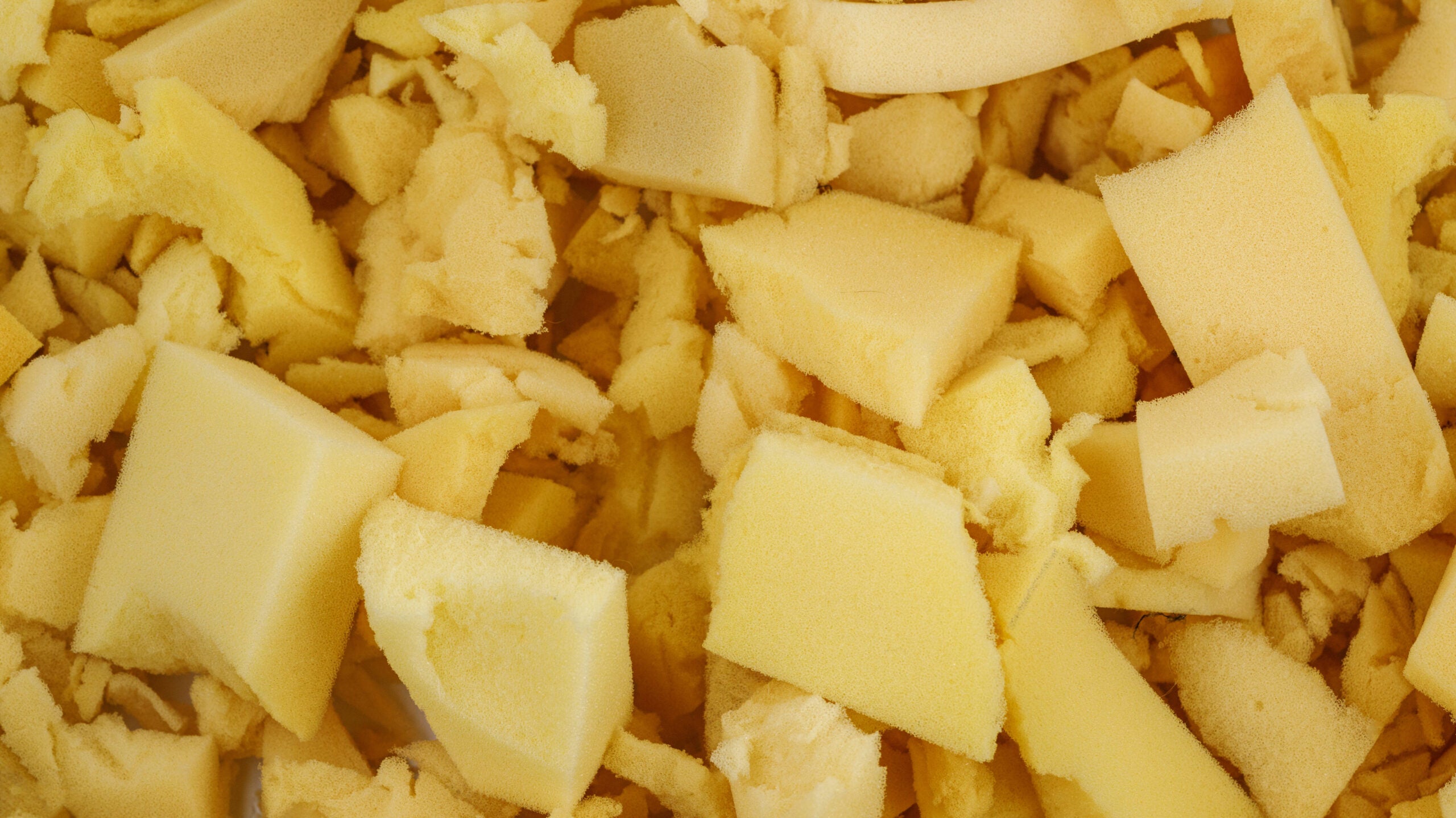
“While municipal recycling is limited to the most common thermoplastics, consumers likely don’t understand the magnitude of the polyurethane problem that needs to be addressed.”
Imidazolysis not only works to break down polyurethanes and allows for recovery of the molecular components (the polyols used to make polyurethanes can be especially valuable to recover), but the physical properties of imidazole also make it a better reagent for carrying out the reaction.
“While I think what we’ve already published on the successful imidazolysis of PET is very exciting,” Bara said, “The chemical recycling of polyurethanes is where imidazolysis may potentially have a much bigger impact.”
This work on recycling PET and PU via imidazolysis has been supported by active funding from NSF and includes contributions from researchers at Iowa State University.